Single-Use Pumps Take Center Stage
The multibillion-dollar global biopharmaceutical industry is placing increased emphasis on development and manufacture of advanced biologics. Such products offer exciting potential for the development of drugs that could provide as-yet-unknown treatments for a wide array of diseases.
One important goal is to commercialize biologic products as early as possible within the typical 20-year patent window. Patent submission must occur during drug development. Much work follows a patent filing, including further product development, toxicity checks, and clinical trials. Hopefully, US Food and Drug Administration (FDA) approval also occurs during this period. Following approval, developers need to take all necessary steps to properly make their products at commercial scale and execute market introduction plans. If a drug’s development takes much time after approval, the patent may run through a good portion of its window of protection before that product has a chance for commercialization. In some cases, only about seven years are left on a product’s patent by the time it goes to market. Every year that a drug is covered by its patent can be worth billions of dollars in sales. So every day that development is accelerated means a greater bottom line.
From a process-equipment standpoint, permanent and single-use quaternary diaphragm pumps — such as Quattroflow pumps — represent a growing technology that helps enable efficient development of new biologic drugs and facilitates speed to market. Single-use pumps (using disposable chambers) feature replaceable wetted parts, which means that no cleaning validation processes (which can require multiple studies) are needed during product development. This is a significant advantage for drug manufacturers seeking to maximize production operations by implementing cutting-edge pumping technology.
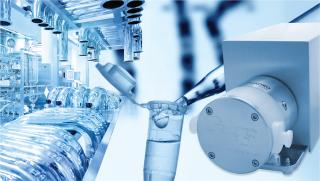
Figure 1: Biologics are manufactured in sterile, time-sensitive conditions. Single-use pumps satisfy product containment and speed-to-market requirements for such operations. ()
“The biopharm industry is adopting disposables faster than the general population is trying to recycle,” said Mark Sitcoske, who heads High Purity New England, a company that specializes in single-use pump technology. Essentially, the driving force in the process to create such products is to promote growth of biologic material in a highly controlled, sterile environment with adherence to strict operating parameters, including the correct pH (acidity) level, temperature, oxygen level, and nutrient feed. An imbalance in any of those parameters can lead to unwanted biologic processes to occur, including growth of competing and undesirable organisms. It could also cause a target biologic process to not occur at all. Once a raw biologic product is produced, desired target components (proteins, molecules) can be purified through a number of techniques, including filtration (e.g., tangential, cross flow, and chromatography), separation (centrifugation), or chemical reactions.
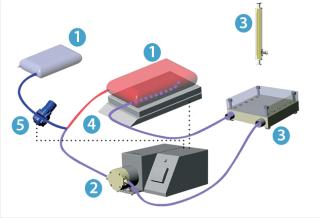
Figure 1: ()
The critical issue in target-component extraction techniques is that biologics are extremely sensitive to change or damage from outside influences such as shear, temperature changes, and light. So the extractionprocesses for target components require a type of pump that can reliably deliver the following operational characteristics:
high purity and sterility
very low volume and surface-area exposure; 15 mL/73.5 cm2 in the smallest pump
low levels of leachables and extractables
no mechanical spalling or shedding of contact materials
controlled, constant flow, as needed
low shear, slip, and collateral effects
low pulsation
self-priming and negative suction lift
controlled pressure
no heat addition
high volumetric efficiency.
Here we describe how one type of pump technology — positive displacement quaternary diaphragm — has become a preferred type to incorporate in critical biologics-handling applications.
The Challenge
Biologic target materials are harvested and purified using separation and filtration processes. The three general purification processes (often used in combination) are described below.
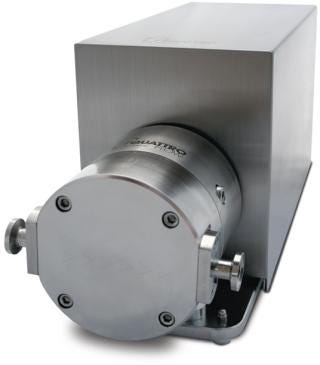
Quattroflow 1200 quaternary diaphragm pump with stainless-steel multiuse pump head ()
Tangential flow filtration (TFF) is also known as cross-flow filtration. For this process, a biologic feed stream flows horizontally with positive pressure across the filter membrane. As it passes across the membrane, the portion of the feed stream that is smaller than the membrane’s pore size passes through the membrane. This is different from what is known as normal-flow (NFF), or “dead-end” filtration, in which the feed flows entirely through the filter membrane with the size of the pores determining which portion of the feed is allowed to pass through and which will remain trapped in the filter membrane. TFF is different from NFF in biologics applications because tangential motion of the fluid across the membrane causes trapped particles to be “rubbed” off — similar to passing your hand across a piece of sandpaper.
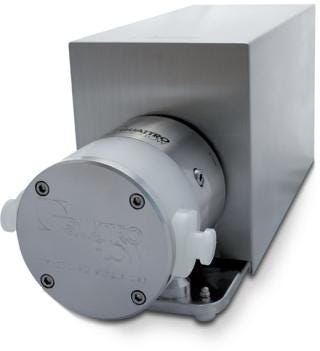
Quattroflow 1200 quaternary diaphragm pump with plastic single-use pump head ()
This mode of operation means that a TFF process can operate continuously with relatively high solids loads without fouling the filter (known as filter blinding). The quaternary diaphragm Quattroflow pump, for example, provides good constant flow control that is essential for optimal filtrate (desired product) yields for TFF filters.
Chromatography Columns: A typical chromatography column is a glass, steel, or plastic tube that is filled with resins compressed in a certain format. A feed stream product flows through it for capture or purification. Such columns contain filter media that need careful handling. A resin, for example, can cost as much as $10,000 per ounce, making proper feeding of it extremely important.
In this type of application, a quaternary diaphragm pump can be used to pack resin into a column and then pump biologic material through that column. Both are critical operations that require a high, constant flow rate and pressure.
Centrifugation: A centrifuge (which is actually a separator rather than a filter) consists of an elaborate vessel that can be fed with a biologic substance and spun around a central axis to separate materials according to their different specific gravities and weights or to separate particles that are suspended in the liquid. A biologic’s target product can be the high, intermediate, or low specific-gravity substance that is spun out of the centrifuge. Because centrifuges spin at high speeds, a proper, constant feed rate is essential to minimize potentially severe vibration that could damage equipment.
In all three processes for target feed-stream purification, pump requirements are precise: constant, low-slip, low-shear, low-pulsing flow. Any deviation from those criteria can result in deleterious effects for a substance being handled and damage media in a filter (membranes for TFF and resins for chromatography columns). Improper flow and transfer rates can also lead to an unbalanced operation that damages a centrifuge.
Pump Types: Over the years, several different types of pump technologies have been used and tested for bioprocessing. Although some are best suited for certain applications, many such technologies have been found to be deficient for the purification processes described above.
Peristaltic (hose) pumps produce pulsation and have limited flow and pressure-handling capabilities. For example, they cannot reliably produce the higher discharge pressures (such as 60 psi) required in some biologic-handling applications. They are also known to release some small quantities of hose material — a process known as spalling — into pumped products, which can compromise product purity. If the shedded hose material is captured by a filter, it can blind that filter, making its operation not as efficient as it should be, and lead to contamination.
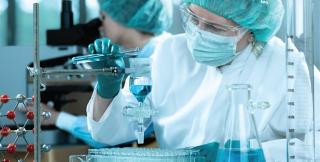
Single-use, low-pulsation, positive-displacement pump options are not suitable for many biologics production processes. ()
Established single-use lobe pump options do not currently exist. Because biologic fluids are contained in a low-viscosity aqueous solution, lobe pumps are not a good match because excessive slip occurs during their operation. That slip can vary between 10% and 100%, depending on a system’s back pressure. This slip will also increase shear damage and energy consumption. If a pump is used in a long-duration recirculation loop (e.g., TFF filtration system), it can noticeably add heat to the product. Lobe pumps also have mechanical seals, which produce a controlled leak that does not provide full product containment unless special seals and seal barriers are used. The sterility required in biologic fluid handling means that no outside contaminants can be introduced into a purification process. That is something that pumps with mechanical seals cannot reliably ensure, unless specific precautions are taken. Such special seals can prove costly to acquire, validate, and maintain.
Centrifugal pumps do not offer positive displacement, resulting in poor flow control when discharge conditions change. Also, high-shear and heat buildup can occur because of relative inefficiencies compared with positive-displacement pumps. Another concern is that some centrifugal pumps are magnetically driven, meaning that instead of mechanical seals, the pumps are coupled and driven by a motor and magnet combination. For single-use applications, disposing of the magnets embedded in other materials presents a problem.
Piston pumps, like lobe pumps, have no mainstream single-use options. Although certain piston pumps can meter with no feedback needed, such pumps are generally complex, leading to higher cost and adverse pulsation and suction conditions that must be managed.
Single-Use Pumps Are Needed
One key manufacturing trend that can reduce development cost and increase speed-to-market is the adoption of single-use technologies. In certain cases, permanent stainless-steel process lines are very costly to set up. They lack the production flexibility needed for biologic development and have complex and time-consuming cleaning and validation requirements. So much expense and time can be saved by simply starting each trial process with a fresh, sterile set of single-use process-equipment components. Such components can consist of bags instead of stainless-steel vessels; special agitators instead of stainless-steel shaft agitators; single-use tubing, couplings, and valves instead of their stainless-steel equivalents; and filter systems, many of which are single-use by nature. Before Quattroflow’s technologies, single-use low-pulsation positive displacement pump options were not suitable for many needed biologics production processes.
“The Quattroflow pump gives you the low shear of a peristaltic pump along with the low-pulsation and high-pressure capabilities of rotary lobes without the inherent dangers and drawbacks of either technology, such as burst tubing, excessive temperature rise, or rubber and metal shavings contaminating the process from upset conditions,” says Jeff Blease, president of Triangle Process Equipment, a pioneering company behind the use of quaternary diaphragm pump technology.
One solution to the strict single-use pumping requirements that are demanded in the biologics-filtering process is Quattroflow’s positive-displacement quaternary diaphragm technology. The company also introduced to the market a single-use configuration. In January 2012, Quattroflow was acquired by the Pump Solutions Group (PSG), which is a conglomeration of several of the world’s leading pump manufacturers that operates within the Dover Corporation’s Dover Energy business platform. PSG has integrated the manufacture of Quattroflow pumps into the operations of its Almatec subsidiary, which is headquartered in Kamp-Lintfort, Germany.
The pumps have a unique form of operation. Quaternary diaphragms aredriven one after another by a connector plate, which moves back and forth out of its central position in a
stroke that is generated by an eccentric shaft. The length of the stroke is determined by the angle of the eccentricity. In other words, this technology has been modeled on the operation of the human heart — which is eminently capable of pumping whole human blood, one of the most shear-sensitive “products” in existence — with its four pumping chambers and check valves keeping product flow constantly moving forward.
The pump chambers contain no rotating parts that can be subject to friction, meaning that there is no operational heat buildup that can compromise a product. This mode of operation also allows pumps to run dry, makes them self-priming, and produces little or no shear because of low slip. In addition, the pumps offer low-pulsation, leak-free operation along with having dry–wet suction-lift capabilities. The pumps can provide constant flows from 1 L/h (0.0047 gpm) to 20,000 L/h (88 gpm) with some of the highest turn up/down capabilities in the industry.
As biologics move from development to clinical trials and commercialization, proper scale-up is essential. The same pump technology used in a laboratory needs to handle flow rates as low as 1 L/h (0.0047 gpm), as well as commercial production flow rates of 20,000 L/h (88 gpm) or more. Scale-up capability ensures that a pump’s operation does not adversely affect process repeatability and production rates.
These pumps also can be fitted with explosion-proof motors, DCA motors, or air motors. You can drive them as you would other pumps. Because of the controlled low-slip aspect and high turn-down capability of this pump technology, it also benefits from a new generations of vector drives for precision applications.
The essential element that contribute to speed to market is a commonality of single-use configurations. Single-use pumps enable biopharmaceutical manufacturers to optimize the cost of cleaning and cleaning validation. The result is not only a faster production process, but one that delivers preferred levels of product purity and sterility with no chance for cross-batch or cross-product contamination.
Here are some other advantages that can be realized when using Quattroflow single-use pumps:
They can be used for one product, or in one production campaign, lasting from one or two days to several months and possibly including a number of batches.
At the conclusion of a production campaign, the pump is removed and its pump chamber that has come in contact with the fluids is disposed of.
A pumo can be used for a set amount of time before its wetted parts are replaced, which eliminates elevated maintenance costs.
It has a removable and disposable plastic chamber that contains the diaphragms.
If an operator needs to use a stainless-steel pump, the plastic pumping chamber can be replaced with a stainless-steel one.
In case of a pump failure, the old chamber can be taken out and replaced with a new one in five minutes, eliminating excessive downtime.
This technology lowers hardware, cleaning, and validation costs.
It can be used when cleaning in place (CIP) or steam sterilization is impractical or impossible, simplifying processes and reducing overall process cost, without contaminated cleaning chemicals and water solutions.
Single-use pumps that are made from FDA/USP class VI conforming and approved materials also have a lower cost than their stainless-steel counterparts. For example, with a 500-L batch of biologics, which has a market value of $5 million-plus and the need to get to the buying public as quickly as possible, an additional $500 or more for a replaceable pump head essentially becomes an attractive cost of doing business. The total cost of using a single-use pump is lower than that of a reusable approach because the cost to replace the head can be significantly less than the cost of validating cleaning and the cost to install a permanent stainless-steel process line.
A common notion in the biopharmaceuticalindustry is that the cost of the paper backing up equipment used is higher than the equipment itself. The Quattroflow pump, by using a standardized and documented single-use variation, reduces that paper and related cost. For cases in which the total cost of a permanent stainless-steel process line is more attractive, a Quattroflow pump head can be converted to stainless-steel head with the same controlled flow, low-shear, low-slip and high-purity operation while adding desirable high-cleanability attributes.
Toward Optimized Manufacture
Advances in the ability to produce and use biologically derived drugs have created an exciting opportunity for biomanufacturers. However, although this continuing trend is packed with possibilities, those can be realized only if the development and manufacturing processes for such products are optimized, both for speed-to-market considerations and contaminant-free production requirements. Quattroflow has identified the challenges in that process and responded with single-use, positive-displacement, quaternary diaphragm pumps that dependably meet a number of challenges. They allow biopharmaceutical manufacturers to confidently meet many of their most crucial biologic handling and manufacturing needs.
About the Author
Author Details
Corresponding author Wallace Wittkoff is global director, hygienic segment responsible for biopharmaceutical technologies at the Pump Solutions Group (PSG), Oakbrook Terrace, IL; 1-502-905-9169; [email protected]. Ravi Prasad is the director of sales at Pump Solutions Group (PSG) India; 91-44-26271020-23; [email protected].
You May Also Like