Celonic’s CHOvolution™ kit comes with a wide range of exceptional services and solutions, on top of high-performance cells. In addition to robust and highly efficient technology, we offer excellent technical support, including comprehensive protocols, audits, tailored workshops, and a 24-7 information access Internet-based platform with a hotline.
For any drug developer or service provider, cell line development is one of the most challenging phases, especially when subsequent GMP compliance is required. To boost and support successful commercial introduction of biological drugs to the market, Celonic has developed CHOvolution™, a cell line kit that can be used for a broad range of applications ranging from non-GMP R&D testing to GMP development and commercial market supply, with a support system to help throughout every step of development.
Celonic: Beyond Manufacturing
Celonic AG is privately owned CDMO based in Basel, Switzerland providing comprehensive GMP development and manufacturing services for n...
In recent years, single-use bioreactors have gained more importance in animal and human cell culture. With its new line of BioBLU frigid-wall, stirred-tank, single-use vessels, Eppendorf offers premium solutions for microbial applications. In the following case study, reproducible process control was achieved with parallel-operated BioBLU 0.3f single-use and reusable glass vessels, both used in an Eppendorf DASbox® mini bioreactor system. Fermentation of
Escherichia coli
K12 led to very comparable results, thus proving tested single-use vessels to be an appropriate tool to accelerate microbial process development and shorten time-to-market in all industries related to microbial production processes.
BioBLU of 0.3f single-use vessel (left) and DASbox mini bioreactor (right)
IntroductIon
Single-use bioreactors are a suitable tool for time- and cost-effective bioprocessing. Minimized setup times, eliminated cleaning procedures, and reduced labor time can sustainably accelerate bioprocess development. In ...
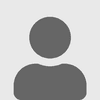
+1Single-use technology has transformed the biomanufacturing industry, because single-use products provide significant savings over stainless steel infrastructure. Single-use technologies also create flexibility for biomanufacturers, enabling them to move from single-product processes to multiproduct facilities. As revolutionary and transformative as single-use technologies have been, the industry is on the cusp of another major shift, which comes with its own impressive benefits, but with some challenges as well.
Continuous and Batch Processing
Continuous processing has been used successfully for many years in a number of manufacturing industries such as in the production of food, chemicals, and steel. When applied to biomanufacturing and combined with single-use technology, continuous processing can offer much higher throughput and increased flexibility.
Batch processing has been the logical method in biomanufacturing for regulatory compliance and quality control. The batch method establishes clear bounda...
Fast and accurate determination of vaccine titer during manufacturing is important for understanding the performance of a development process and for scaling each process step. Although single radial immunodiffusion (SRID) has been the most commonly used technique for vaccine titer determination, it can be time-consuming and imprecise, requiring up to three days for results. The Pall ForteBio Octet® system offers a simple and direct method for measuring vaccine–antigen–antibody binding, capable of delivering high-precision analysis in as little as three hours.
Table 1: Comparison of Octet system with single radial immunodiffusion (SRID); B/Massachusetts influenza virus
Methods
Using the influenza virus as a model system, the relative standard deviation and dynamic range of a vaccine titer assay were measured with the Octet system and compared with results from using SRID. Polyclonal serum antibodies were loaded onto Octet biosensors, and their binding measured to epitopes presented by an inactivated virus...
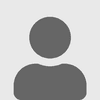
+1Efficient expression of proteins is an integral part of the biopharmaceutical drug development process. With a range of expression systems, it is important to balance long-term manufacturing goals (e.g., cost of goods and productivity) while matching the expression system to suit the characteristics of a protein (e.g., product quality attributes and long-term stability). Finding the right expression system early on can make or break a therapeutic candidate as it moves from laboratory bench to clinical administration.
FUJIFILM Diosynth Biotechnologies has developed its pAVEway™ expression technology to support microbial expression of proteins. This platform technology incorporates three elements in the delivery of an
Escherichia coli
expression process: optimized expression vectors and control elements, preselected host strains, and platform development using a high-throughput approach for fast strain selection and/or design of experiment (DoE) approaches.
DNA looping in pAVEway™ expression technology is...
Today algae are commercially cultivated for pharmaceuticals, nutraceuticals, cosmetics, and aquaculture purposes.
The abundance of vitamins, minerals, and trace elements as well as the fatty acid profile and thickening and stabilizing functions of their polysaccharides make algae valuable. Algae also can be used to produce biodiesel, bioethanol, and biomass that can be burned to generate heat and electricity. Like plants, algae use sunlight during photosynthesis. Photosynthesis is an important biochemical process in which plants, algae, and some bacteria convert the energy of sunlight to chemical energy. Algae capture light energy through photosynthesis and convert inorganic substances such as CO
2
into simple sugars or oils using the captured energy.
KIT laboratory
Several factors (e.g., light, temperature, pH, nutrients, aeration, and mixing rate) can be measured to determine the growth rate of algae. To optimize yield, algae is cultivated in closed photobioreactors. Within those, process conditions c...
Many biopharmaceutical manufacturers are implementing single-use containment for transfer of media and buffer materials to prevent feedstock contamination and promote worker safety. But the type of containment system used can have a significant impact on productivity and profitability. Equipment should be evaluated and chosen carefully.
Pertinent Questions
Systems should be analyzed not only for their basic ability to contain powders of interest, but also for how efficiently they integrate into production process. For instance, could the system introduce productivity bottlenecks, increase material waste and the cost of raw materials, or complicate changeover of a line to new products? Is it robust enough to provide reliable transfer throughout the production run? And has it been designed specifically to contain and release powders? The answers to those questions are crucial to identifying and implementing a sound powder-transfer system.
Issues of Powder Handling
Media and buffer ingredients used in powd...
The need for a rapid turn-around in quantity (and the loss of technicians in many laboratories) has created a trend toward implementation of single-use vessels. Their advantages include no time lost in cleaning or sterilization (especially for bench-scale, autoclavable systems), no chance of inhibition or cross-contamination due to poor cleaning, and no need for cleaning and sterilization facilities in a crowded laboratory.
For production-scale steel bioreactors, fully automated clean-in-place (CIP) and sterilization-in-place (SIP) have been possible for decades. By contrast, bench-scale systems required considerable downtime for disassembly, cleaning, reassembly, autoclaving, and cooling before use — with no guarantee that each step was carried out correctly and reproducibly. An innovation from INFORS HT brings the advantages of CIP/SIP to bench-scale bioreactors, offering a true alternative to single-use systems for microbial applications.
Table 1: Sterility testing against a panel of highly resistant t...
For over 75 years, Kerry has earned its reputation for reliability and excellence in serving the biotechnology, pharmaceutical, and nutrition markets. We deliver innovative solutions to assist customers increase cell proliferation, extend cell viability, and increase target protein production in biotechnological production systems.
Figure 1: Viable cell density and IgG titer in CHO DG44 cell line
Every day, we expand our capabilities to meet the changing needs of the biotechnology market. Kerry’s products have evolved with market trends in cell culture over the past 50 years to fulfill our customers’ requirements and have grown to encompass modern plant-based hydrolysates, yeast extracts, recombinant proteins, cell-line–tailored supplement systems, and chemically defined media. Kerry has the vast global resources and technical platform to deliver consistent, high-quality products backed by unparalleled service, technical support, and formulation customization capabilities.
Chinese hamster ovary (CHO) cell...
During the fall of 2014, we received requests from a couple of large, single-use technology (SUT) system integrators asking whether we could develop a new tube clamp for their SUT assemblies and skids. There were several motivating factors behind these requests. As bioreactor skids became larger and larger (with thousand-liter and larger SUT containers), technicians had increasing difficulties assembling current clamps onto tubing. In some cases, technicians were lying on their stomachs and reaching under the bioreactors trying to install clamps. In other cases, they were standing on tall ladders or platforms reaching across the tank and container to access tubing.
PharmaLok™ tube clamps during the long-duration pressure test
After discussing the technicians’ needs in more detail, we came away with a list of challenging requirements for a potential new product. The number-one desire was for a clamp that can be easily opened and closed using just one hand. This would simplify assembly while technicians rea...
A finalist for the 2012 BPI Technology of the Decade Award, XCell™ ATF systems consistently yield high cell retention, concentration, and viability, enabling efficient and productive perfusion and
N
– 1 perfusion as well as cell banking and seed-train cell culture operations.
Figure 1: Scalable from laboratory to production: XCell™ ATF systems include the device and controller. XCell™ ATF single-use device (left) are available in two sizes. XCell™ ATF stainless steel device (right) are available in five sizes.
XCell™ ATF devices are now available in single-use format, in addition to stainless steel. The new single-use devices deliver 100% cell retention and laboratory-to-production scalability like their stainless steel counterparts but without the need for autoclave sterilization and lengthy setup times.
Figure 2: Alternating tangential flow (ATF) technology: XCell™ systems use ATF technology created by the action of a diaphragm moving upward and downward within a pump head, connected to a filter housi...
Modern, automated peptone production
Peptones from the Solabia Group represent the result of nearly 50 years of strategic activity and savoir-faire. As key components in industrial fermentation, they contribute to a range of products, from probiotics and vaccines to specific bacterial metabolites in cosmetics. Although they are often perceived as replaceable commodities with similar sounding names, that misconception can lead to significant problems. Peptones differ in sourcing as a function of a producer’s manufacturing experience, raw materials, and (most important) production site itself and its level of technical advancement. The more modern the site, the greater the likelihood that it can produce consistent, high-quality peptones.
Dual Production Sites and Animal Separation Set Solabia Apart
Solabia separates animal tissue processing from its plant and casein manufacturing, which is unique to the peptone industry and an important part of eliminating cross-contamination. Solabia’s production site for ...